BUCKLE MOTORS
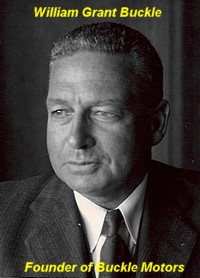
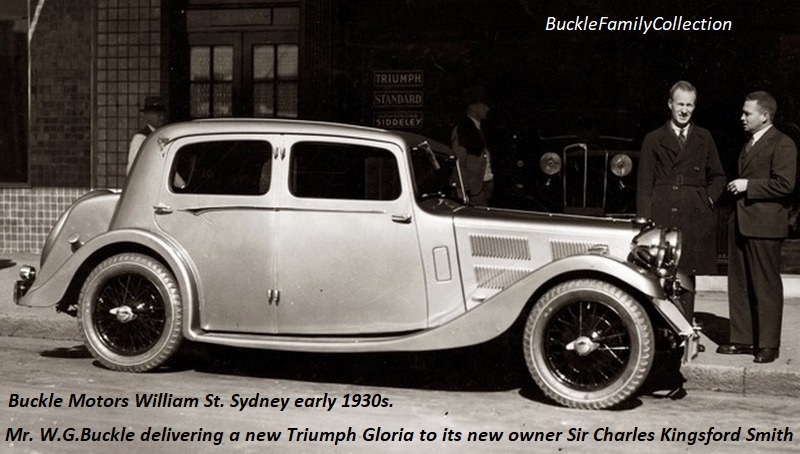
Buckle Motors new Punchbowl factory being built in the mid 1950s
The birth place of the Buckle Coupe and the Goggo Dart
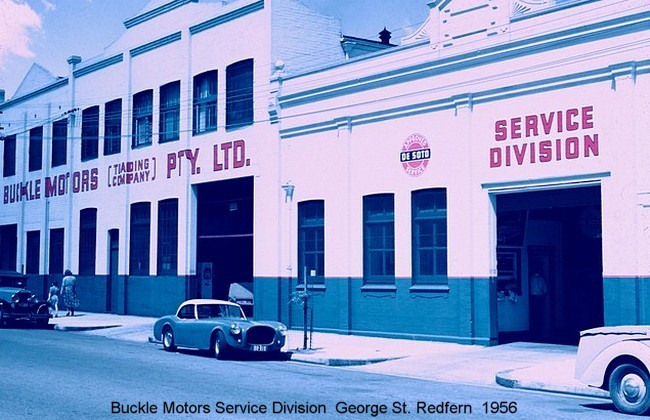
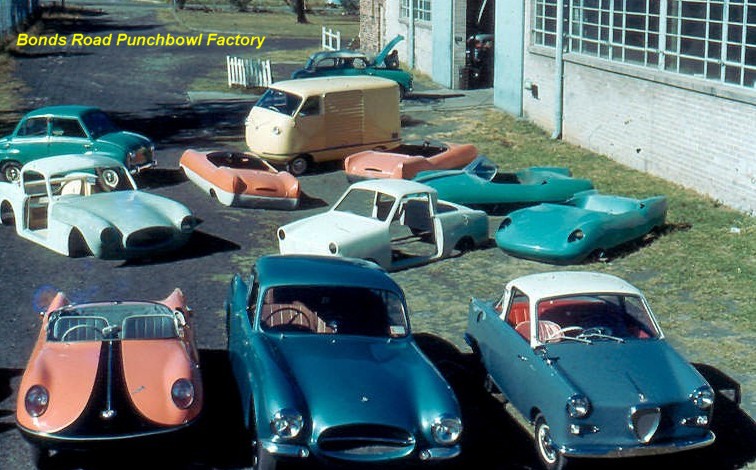
Originally Buckle Motors started selling new Amilcars in Melbourne around 1924.
Then came to Sydney were they took on the new car dealerships of Triumph, Talbot, Armstrong Siddley, De Soto (1934), Citroen (1949), Goliath -Hansa, Borgward, Hillman, Humber.
Bill Buckle in 1955 built a Buckle Convertable with a detachable roof, then in 1957 released the first production Buckle Coupe.
After this he made the bodies and assembled the German designed Goggomobil sedan, coupe & van..
His pride and joy Goggo was the Dart sportscar which he designed and built many of these.
Next came the Right Hand Drive Conversion company which converted 100's of American cars LHD to RHD.
And in Bill's spare time he built up one of Australia's top Toyota Dealership. Bill Buckle Toyota at Brookvale.
Today (2012) Bill still enjoys his cars and boats.
Interview with Bill Buckle, by Athol Yeomans for Wheels Magazine, August, 1960
Local Firm Becomes Worlds Second Biggest Fibreglass Car Producer .
FIBREGLASS - FIVE TIMES PROVED.
Here is Bill Buckle's own story of how he and his team got fibreglass cars out the the books and onto the road.
The people responsible, Buckle Motors of Sydney, NSW, are now, in fact, the largest outfit of its kind in the world, bar one - Chevrolet's plastic Corvette plant. Other people produce plastic cars, in ones and twos. Plenty of people say they intend to, in larger quantities. Somehow, they seem to get bogged down and they never get into production. But Buckles have overcome the fantastic troubles and difficulties and have, as they say about these things, 'arrived'.
Like most successful motoring ventures, the fibreglass idea started as nothing much more than wishful thinking by the general manager, W. Lowrie, and Bill Buckle, son of the late William Buckle, who founded the show in the thirties. The wishful thinking was for a really good Australian sports car which would offer genuine, as opposed to theoretical, performance, with a few practical things like ample luggage accommodation thrown in.
Our firm, Buckle Motors Pty Ltd., are old-established motor distributors. We have sold Citroen, Armstrong-Siddley and De Soto cars and trucks in the past, all usccessful and well-established names. Our fibreglass venture had not even been thought about, although the idea of a good local sports car had been discussed on many occasions.
Then I went abroad to learn more about the motor business, and in 1953 saw what was then a complete novelty - a plastic body at the London Motor Show. It interested me straight away because, although I felt we could design and build a good sports car chassis, the body would be a problem. Hand-made aluminium bodies would be far too expensive on a series production basis, and unless it was a series-production car it wouldn't be of much use commercially. Steel bodies were right out from the word go because of cost. A set of dies, from which a steel body is pressed, certainly wouldn't cost less than $500,000 and if the production department were given their head they could cost $2,000,000.
Anyway, fibreglass seemed to be the key to our dream. I found out all I could about the techniques and came back to Australia with the intention of persuading the other directors of the firm to give me the green light. I persuaded them all right, but there have been times since when I think it might have been better if they had cut my throat instead. However, everybody has their problems. Most of 1954 and 1955 went into designing our prototype sports car.
Fortunately, I had driven in races and trials a lot in Citroens and from my own experiences and those of other drivers, I knew what was wanted - a closed car with comfort and luggage room, plus real performance and first-class handling. Like the production car, the prototype met these demands with Ford Zephyr mechanical components, a straight-rail chassis, live rear axle and independent front suspension, plus the all-important fibreglass body - our first.
We made it by doing some rough sketches on paper, then building a little model of what our sketches looked like, and from that building a full-scale plaster of paris model of the car. You may think it sounds fairly straightforward. So did we, until we tried. However, after spending several thousand man hours on the job we knew differently. Firstly, we had to get a shape which looked pretty right. Then we had to combine that with an envelope to contain people, luggage, engine and other mechancical parts. We had to arrange it so that there was room to get at all the components, and that a mechanic wouldn't have to take the car to pieces merely to make a simple adjustment - one of the bugbears of limited-production cars. So we changed and altered and covered ourselves and the shop liberally with plaster of paris.
The first prototype was produced in the middle of 1955, after our first experience of fibreglass moulding. When the model was finished, we covered it with release agent, so that the plastic and fibreglass would not stick to the plaster, then built up on it our mould, which is a negative impression of the finished car - like a cake tin used to turn out a cake. The mould is made of the same materials which go to form the finished body - polyester resin - which comes in liquid form in tins, and fibreglass, which is a loose mat-like material formed from thousands of finely-drawn glass fibres. Glass in this form is immensely strong while being soft and feathery to the touch.
To make the mould, a layer of resin was brushed on over the finised plaster mock-up. While still tacky, a layer of fibreglass mat is laid on it, with smaller pieces tucked in the odd corners to cover the job evenly. Another layer of resin was brushed on, followed by more fibreglass, and this proocedure was repeated until the mould was thick enough and strong enough. It was allowed to set hard, which takes only a few hours, and then the plaster model was removed, in pieces, from inside it. The plaster does not stick to the fibreglass because of the covering of release agent.
Although the mould was quite hard, it was left for several days while the curing process went on. Fibreglass takes several weeks to attain its full strength, but it can be worked in just a few hours after manufacture. Nowadays, to accelerate the curing process, we use a heat-controlled oven where the temperature is maintained at 150 degrees F.
As we expected, we had a lot of hand finishing work to do on the mould - touching up where the mould was not quite perfect, reinforcing it so that it would support the weight of the body material which would be laid up in it.
From the outside, the mould didn't look much like a car at all. The smoothly-finished surfaces were on the inside. The mould itself was divided in several pieces, so that the body shell could be made in one piece, leaving nothing to add but the bonnet and doors. In this prototype, and in the production car which followed, the floor, sides, tail and, in the later car, the roof, were all in one piece.
After we got the mould right, we laid up the actual car body inside it, repeating the procedure of alternate layers of resin and fibreglass. Then, when this has cured, we unbolted the external mould and laid bare our first fibreglass car.
It was a two-seated open car, similar in appearance to the present Buckle. As soon as it was completed we began to work out changes to its styling, but in the meantime we had a tremendous amount of work to do on the chassis. No major changes were made, but there was a lot of experimenting to do before we passed it as satisfactory.
The chassis frame itself is made up of two longitudinal members, 5 in. x 2 in. fully boxed and swept up over the rear axle. The cross members number six in all, three tubular and three square sections. The front suspension is by a transverse leaf spring at the bottom and wishbones at the top. As a safety measure the second leaf is wrapped around the rubber-bushed lower swivel pin support, in case the main leaf fails. In transverse leaf suspensions this allows the wheel to collapse.
Lever-action shock absorbers are fitted, primarily because they fitted easily into the suspension layout, but also because they enabled us to experiment with the valve settings inside. The spring rate finally settled on was harder than touring car springs, but not as hard, for instance, as the older type of sports car such as the TC.
Rear suspension is by an ordinary live axle and leaf springs. These are inclined towards the front of the car to promote understeer. The engine and gearbox are proprietary Ford Zephyr components, as is the back axle, brakes and auxiliaries.
All up, the finished car weighs 17 cwt. with oil, spare wheel and tools and a minimum amount of petrol in the tank. Braking area is the same as the Ford Zephyr at 147 sq. in. The brakes have always given excellent results.
Power is pretty well what the customer wants. The standard Zephyr engine develops 86 b.h.p. on 7.8 to 1 (at 4,200 r.p.m.) Cars we have delivered fitted with the Raymond Mays six-port heads and two carburettors develop 127 b.h.p. and with overdrive fitted the car in this form will reach 120 miles an hour. My own car obtained 128 m.p.h. The price of the head adds 1,000 pounds to the price of 1800 pounds.
In competition the car has done well, the most recent run being that of Clive Kane who, at his first ever hill climb was within half a second of Geoghegan's best time in his Holden, which I think everybody will admit is probably the fastest one there is.
But to get back to fibreglass ..... and its problems and advantages. When we built the prototype we were able to assess both sides of the story, and there is no doubt that it is a very good material for car work. It is about half the weight, strength for strength and size for size, as steel. Two men can carry a Buckle body. Unlike steel, fibreglass does not crumple, but bounces back into position. In fact, one of our gimmicks was to pound the car with a tyre-setting hammer to show its properties. If the blow is too severe for the material - as in a bad crash - the fibreglass breaks, but will not lose its shape. Repairs are made by patching the cracks with resin and glassfibre. It is also a sound-deadening material, which saves on insulation and reduces drumming.
The disadvantages are nil from the user's point of view, but they give the manufacturer some headaches. We had all sorts of difficulties learning the best way to get the best finish. Early on we found that the pattern of fibreglass showed through to the surface, and we also had trouble with little air bubles marring the finish. Both these have been overcome.
By this time we felt confident enough to make up a production car. Alterations to the styling were done by modifying the original plaster mould, and a coupe top was added. Our first production car was ready in June, 1957, and they have been produced steadily ever since.
BUCKLE MOTORS NEW CAR DEALERSHIPS
from 1924 to now
Buckle Motors Sales Pty Ltd.
Buckle Motors Trading Company Pty Ltd.
Buckle and Harden.
Bill Buckle Toyota.
Bill Buckle Conversions
Buckle, Citroen, Armstrong Siddley, De Soto cars & trucks, Goliath-Hansa, Goggomobil,
Amilcar, Lloyd Hartlet, Borgward, Triumph, Talbot, Hillman, Humber, Toyota, Audi, VW, Subaru.
Buckle Motors issued Classification Plates to every new vehicle they sold.
The first 2 or 3 numbers indicates the manufacturer/model of the vehicle...eg. Buckle Coupe 93-???.
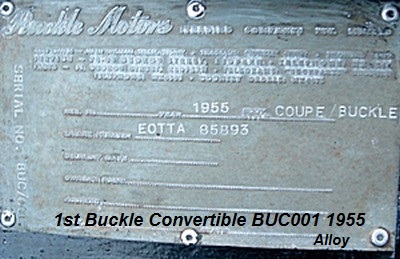
Here is some of the old advertising from car magazines and newspapers
|